Digital? Oder Lean?
Unsere Antwort: Digital und Lean!
Warum Lean und Digital keine Konkurrenten, sondern Kollegen sind. Und wie sie durch die clevere Kombination von Digital und Lean viel mehr erreichen als mit Lean oder Digital alleine.
Digitalisierung ist in der Praxis angekommen und längst kein Thema mehr alleine für große Konzerne. Zu Recht, angesichts der Vielzahl an Chancen und Möglichkeiten für die Effizienzsteigerung operativer Prozesse, die mit dem Einsatz neuer digitaler Technologien verbunden sind.
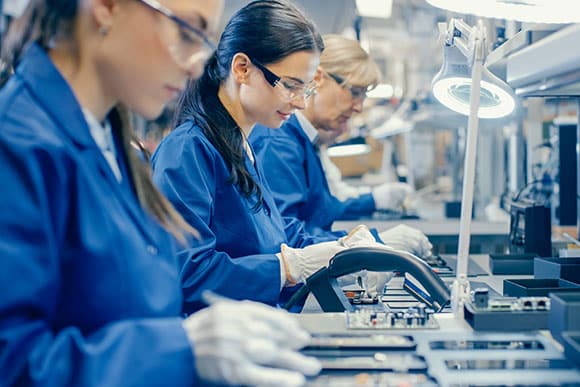
Vor kurzem sagte ein Kunde
Folgendes zu einem unserer Berater:
“Die Methoden und Vorgehensweisen, die Sie für OEE-Steigerung vorgeschlagen haben, sind alle sinnvoll. Das brauchen wir und das würde unser Unternehmen deutlich voranbringen. Aber es gibt ein Problem: das sind sehr viel Lean-Themen mit dabei. Bei uns werden aktuell keine Budgets für Lean oder Workshops freigegeben. Budgets gibt es nur für Digitalisierungsprojekte.”

Was uns zu folgenden Fragen führt:
- Gibt es wirklich ein „entweder oder“ bei Digital und Lean? Sind Digitalisierung und Lean wirklich zwei gegensätzliche, sich wechselseitig ausschließende Konzepte?
- Muss man sich entscheiden, ob man ein Lean-Projekt oder ein Digitalisierungs-Projekt macht?
Es lohnt sich hier genauer hinzuschauen, weil wir in unserer Beratungspraxis eine solche harte Trennlinie nie wahrgenommen haben. Nach unserer Praxis-Erfahrung ist die Antwort eindeutig: Digital und Lean / OpExc sind keine Konkurrenten. Sondern im Gegenteil, Digital und Lean sind komplementäre, sich sehr gut ergänzende Konzepte, die wie Puzzle ineinandergreifen, und im Zusammenspiel mehr erreichen, als bei einer alleinstehenden, isolierten Anwendung.
Digitalisierung ergänzt den bestehenden Methodenbaukasten Lean/OpExc mit sehr mächtigen, wirksamen Tools und Möglichkeiten. Manchmal legen neue Digitalisierungstools ein starkes Fundament, auf dem mit Lean / OpExc weiter aufgebaut werden kann. In anderen Fällen ist es s es sinnvoll, sehr oft auch notwendig, mit „klassischen“ Verbesserungsmethoden wie Workshops, Fluss, Methoden anzufangen um dann erst wirtschaftlich rentabel Digitalisierungslösungen anzustreben. In fast allen Fällen gilt: erst durch das Zusammenspiel, durch eine clevere Kombination können Sie die besten Effekte erzielen. Und manch teure Digitalisierung, die auf unreife, instabile Prozesse aufsetzt, hat sich im Nachhinein als teure Fehlinvestition herausgestellt – nicht weil das Tool schlecht wäre, aber weil wichtige Aufbau-Beziehungen und Fundamente nicht berücksichtigt wurden.
Abstraktes Prinzip – konkrete Beispiele aus unseren Projekten:
Office Prozesse: Process Mining, Prozessworkshops, Robotic Process Automation:
Office-Prozesse mit Process Mining, einer Softwarelösung zur belastbaren und detaillierten Ist-Analyse ihrer Prozesse in Bürobereichen, wirkliche (nicht geplante / dokumentierte) Abläufe mit Zahlen, Zeiten zu verstehen ist eine hervorragende Plattform für nächste Schritte: Die so gewonnene Transparenz ist notwendige Voraussetzung für die anschließende Verbesserung.
Aber auch nicht mehr als das.
Office-Prozesse zu optimieren, die oft extrem hohen Anteile Verschwendung zu reduzieren, minimalen Durchlaufzeiten zu schaffen, das können sie nicht mit einer Software: Das geht nur zusammen mit Mitarbeitern, das erreichen sie nur durch Prozessworkshops mit den Mitarbeitern aus den Prozessen. Hier klären Sie Ursachen und Hintergründe für erkannte Probleme, und erarbeiten zusammen Lösungen, zukünftige Soll-Zustände Maßnahmen. Im Rahmen dieser optimierten Prozesse haben sie dann viele weitere Digitalisierungs-Chancen, So können Sie zu Beispiel durch Document Capture, Workflow-Systeme oder Robotic Process Automation völlig neue Level der Produktivität, Geschwindigkeit und Effizienz erreichen. Kriegsentscheidend ist aber auch hier die Reihenfolge das Vorgehens: nach dem Motto „Shit in – Shit out“ es hat sich nie bewährt zu versuchen, instabile gewachsene Prozesse durch den Einsatz von IT zu optimieren.
Oder nehmen wir zum Beispiel Tools für digitales Shop Floor Management (SFM):
Klar ist, dass SFM-Lösungen die auf Papier und Zettel, oder auch auf reinem Excel basieren, nicht mehr zeitgemäß sind –zu hoch ist der manuelle Aufwand für Datenerfassung, Ausdrucke, zu hinderlich ist oft auch die zeitliche Verzögerung zwischen Auftreten und Aushang. Digitale Lösungen, die z.B. auch gleich noch Maßnahmen-Workflows / Maßnahmen-Monitoring integrieren sind erheblich im Vorteil gegenüber allen analogen Systemen.
Trotzdem ist SFM beileibe kein IT-Thema: SFM ist ein zentrales Scharnier zwischen Shopfloor und Management, zwischen Verschwendung und vor allem Verbesserung. Diese Verbesserung ist Teil einer Kultur, setzt nicht nur Führungsfähigkeiten, sondern auch Wissen zur strukturierten Verbesserung voraus, wie z.B. Lean, Fluss, Verschwendung sehen, Pull-Konzepte, Qualitätsverbesserung, Standard-Problemlösungsprozess, usw.
Unser Fazit zu SFM ist: zu 80% geht es um Menschen. Wissen. Strukturen. Know-How. Maximal 20% des langfristigen Erfolgs stecken in der der Digitalisierung.
Das ist umso aktueller und wichtiger, als es gleichzeitig einen Trend gibt, dass auf Basis der nun digital leicht verfügbaren Daten oft immer mehr Auswertungen, Kennzahlen, Reports erzeugt werden, einfach weil es mit digitalen SFM-Tools sehr schnell und unaufwändig machbar ist.
Bedeuten mehr Kennzahlen automatisch mehr Verbesserung? Bei vielen SFM-Systemen, die wir in unserer Praxis sehen, stellt sich heraus, dass das Gegenteil der der Fall ist: sehr oft setzen zu viele Kennzahlen falsche Prioritäten. Das eigentliche SFM-Ziel, das kontinuierliche Erkennen und permanente, wirksame Verbessern von Shop-Floor-Problemen tritt im Vergleich zu Kennzahlen / Report sehr oft in den Hintergrund. Das war so sicher nicht im Sinne des Erfinders. Digitalisierung von SFM ohne wirkliche, strukturierte Verbesserung von Verschwendung und Problemen ist kein rentables Projekt.
Weiteres Beispiel: OEE-Verbesserung.
Bei OEE-Verbesserung gehen Digital und Lean Hand in Hand, digitale Datenerfassung und Lean-Ansätze zur Verbesserung funktionieren erst in ihrer Zusammenarbeit richtig: Wirksame OEE-Verbesserung gründet immer auf Daten, auf belastbarer Transparenz zu tatsächlichen Verlustursachen. OEE-Software, MES-Systeme oder auch iIoT-Plattformen helfen dabei diese Daten viel schneller und genauer zu erfassen als früher in analogen Systemen.
Diese Transparenz ist absolut notwendige Grundlage, um dann die richtigen, vulgo: wirksame und rentable Maßnahmen für die OEE-Verbesserung zu definieren und umzusetzen. Solche Maßnahmen sind z.B. Maschinen-Defektworkshops und TPM, SMED, Mitarbeiter-Qualifikation, Qualitätsworkshops und -projekte. Für die eigentliche Verbesserung von erkannten Prio-Problemen funktioniert immer nur zusammen mit Menschen, mit Lean-Methoden, Workshops, etc. Auch für OEE gilt: Datenerfassung (egal ob analog oder digital) ohne Verbesserung ist Verschwendung.
Gleichzeitig eröffnet die Online-Erfassung von Maschinendaten auch völlig neue Türen und Chance, z.B. für den Einsatz von Konzepten der vorbeugenden Instandhaltung oder Predictive Maintenance. Chancen die es ohne Digitalisierung nicht gibt.
Oder betrachten wir als Beispiel Prozesse in Instandhaltungsbereichen, die häufig geprägt sind von Schnittstellen, analoger Datenverarbeitung und Informationsflüssen: Digital Smart Maintenance-Systeme digitalisieren die Prozesse in der Instandhaltung, sind der wesentliche Treiber auf die Instandhaltung-Effizienz /-geschwindigkeit und damit auch auf die OEEs ihrer Anlagen. Digital Maintenance Software kann aber nicht das Wissen, die Projektarbeit zur effizienten Organisation, zur Gestaltung richtiger Prozesse in Ihrer Instandhaltung ersetzen – man muss vereinfacht gesagt, diese Tools mit ihren Möglichkeiten auch einsetzen können.
Es gibt noch viele weitere spannende Beispiele dafür wie ein gutes Zusammenspiel aus Digital und Lean wirklich funktioniert, die hier aus Platzgründen nur kurz betrachtet werden können: Logistik zum Beispiel, wo ein Pick-by-Light hervorragende Chancen zur Steigerung Ihrer Kommissionier-Effizienz bietet, aber grundlegende Tugenden wir Ordnung / Sauberkeit, Spielregeln, Stammdatenpflege nicht mal annähernd ersetzen kann. Oder Montagen, in denen mit visueller Werkerführung und Cobots optimiert wird. Während gleichzeitig in genau denselben Montagen Vorgabezeiten nicht passen, Qualitätsprobleme / fehlendes Material aus vorgelagerten Bereichen Produktivität kosten, es zu >30% Taktzeitverlusten aufgrund schlechtem Line-Balancing kommt, … Der Einsatz digitaler Tools in der Montage eröffnet neue Chancen zur Steigerung von Effizienz und Qualität, aber die Digitalisierung ist kein Universal-Werkzeug, dass alle bestehenden Problemursachen beheben kann. Auch in Montagen gilt ganz klar: Digitalisierung und Lean ergänzen sich, schließen sich keinesfalls aus. Wie Sie in welchen Reihenfolgen vorgehen, um schnell die besten Pay-offs aus den Ihren Investitionen in die Verbesserung zu erzielen, wird immer von Ihrer Ausgangsituation und Ihren größten Verbesserungshebeln abhängen. Wir empfehlen nie, Digitialisierungs-Projekte zu machen, weil „man gerade Digitalisierung macht“. Gestalten sie einen individuellen Mix aus Digital und Lean, aus IT und Mensch, Workshops, Schulungen und Projekten – Sie werden schneller zu besseren Ergebnissen kommen.
Fazit:
Digital? Oder Lean? Unsere Antwort ist eindeutig: Lean und Digital!
Weder mit Lean alleine noch mit Digital alleine werden sie alle Chancen und Potenziale realisieren, die in Ihren operativen Prozessen noch vorhanden sind.
Digitalisierung ergänzt den „klassischen“ Methodenbaukasten Lean / OpEx, schafft mit neuen Technologien völlig neue Chancen, die es früher nicht gab.
Lean und Digital – in den richtigen Reihenfolgen, miteinander kombiniert und verzahnt, aufeinander aufbauend. Das ist Verbesserung, die sich rechnet, die schnell und nachhaltig wirkt
Und unser Kunde, bei dem es nur Digitalisierungs-Budgets gibt?
Wir hatten zum Glück die Chance für ein gemeinsames Meeting mit dem CFO des Kunden. In der gemeinsamen Diskussion wurde ein gemeinsames Verständnis dafür erzielt, dass die digitale OEE-Datenerfassung für Transparenz wichtig ist. Das aber Transparenz alleine ohne die ohne die anschließende tatsächliche Verbesserung durch Defekt-Workshops, SMED, Qualitätsverbesserung ein teures Investment mit sehr schlechter Rentabilität ist.
Im gemeinsamen Projekt, das im Nachgang zu diesem Meeting freigegeben wurde, konnte unser Kunde mit clever kombinierten Digital- und Lean-Tools eine Steigerung der OEE an Engpassanlagen um mehr als 15% erreichen, höhere Umsätze realisieren und seinen EBIT um rund 2,5 Prozentpunkte steigern. Das Projekt war nach Aussage des CFO „eines der rentabelsten Projekte in der Unternehmensgeschichte überhaupt.“
Wir begleiten Sie dabei, das Beste aus beiden Welten zu kombinieren. Wir sind ihr Navigator durch den Dschungel der Vielzahl an digitalen Tools und Möglichkeiten, wir zeigen Ihnen wie Sie im Zusammenspiel beider Konzepte die besten Ergebnisse erzielen. Ob es um Verbesserungen bei Ihren Maschinen/Anlagen, in Ihren Montagen oder in der Produktionslogistik geht –profitieren Sie von unserer Erfahrung und Expertise aus tausenden Projekten weltweit. Sie erhalten genau die Beratung, Begleitung und Lösungen, mit denen Sie und Ihr Unternehmen schnell und wirksam das nächste Performancelevel erreichen. Und Sie profitieren von Verbesserungssprüngen bei EBIT, ROI, Umsatz, Kundenbindung und Margen.
Kontaktieren Sie uns
Jörn Tegtmeyer
Geschäftsführender Gesellschafter Telefon: +49 (0) 89 23032325 E-Mail: jtegtmeyer@leonardo-group.com |
Erfahren Sie, wie die clevere Kombination von Lean und Digitalisierung die Produktivität in Vormontagen um über 40% gesteigert hat.
Jetzt downloaden